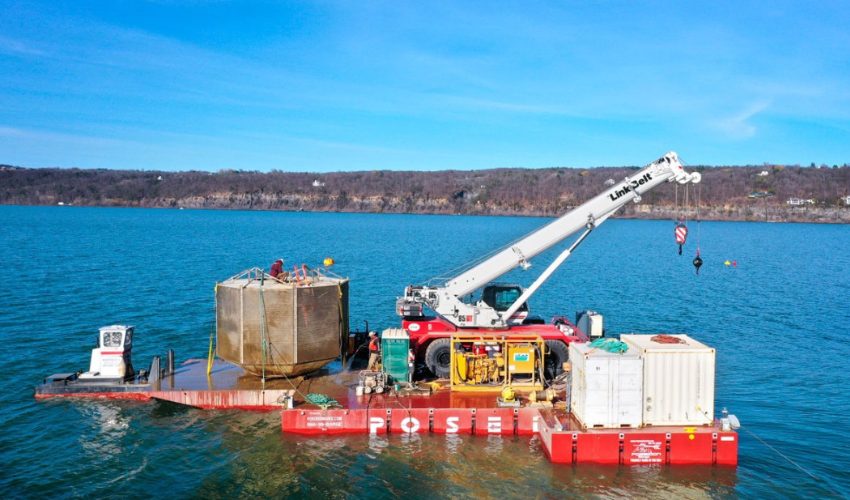
Sustaining sustainability on a big campus could be a complicated problem, as balancing environmental duty with environment friendly operations requires revolutionary options. Final week, Cornell College’s Lake Supply Cooling (LSC) system underwent important upkeep to fight the challenges posed by invasive mussels and particles. This undertaking has seen the combination of revolutionary 3D printed parts, highlighting a collaborative effort amongst engineers, college students, and cutting-edge 3D printing expertise.
The LSC system, which leverages the icy depths of Cayuga Lake for cooling, has considerably lowered electrical energy consumption and general prices for Cornell College and Ithaca Excessive College. This has saved the establishments greater than 20 million kilowatt hours of electrical energy per yr with out using refrigerants or the discharge of poisonous greenhouse gases. Nonetheless, the buildup of zebra and quagga mussel colonies has threatened the system’s effectivity by drastically lowering water move, requiring periodic, however intensive upkeep to make sure its continued operation at peak efficiency.
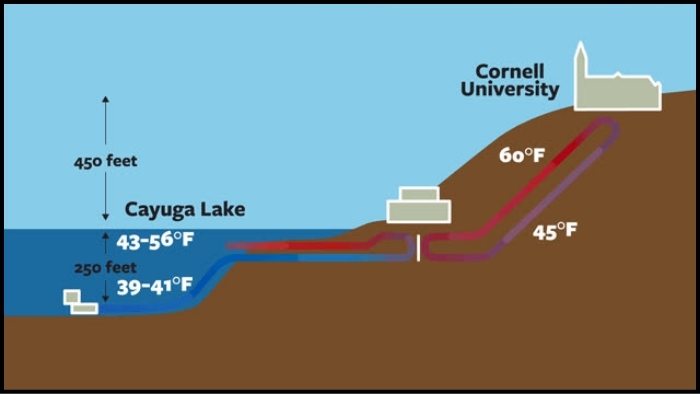
The Lake Supply Cooling System of Cornell College.
Usually, step one of this upkeep course of includes hooking chains to the big metallic display of the LSC, submerged 250 beneath the floor of Cayuga Lake. The attachment permits the display to be raised from the lake ground for cleansing. Nonetheless, after a number of failed makes an attempt to align the chains with the display, it turned evident that Cornell College required an revolutionary answer. Turning to the benefits of 3D printing, Cornell decided it to be the optimum device for enhancing effectivity in the course of the operation.
Led by engineering scholar Mark Tarazi, the undertaking started implementing using 3D printed thermoplastic items. This allowed for straightforward and fast alignment and attachment of the display to the chains. Tarazi spoke on the undertaking’s success, stating, “It’s actually cool to see it in motion. We don’t normally get to see the tip undertaking or how our half matches into it. It was actually significant to see that we’re making a distinction.” From right here, the subsequent step within the upkeep course of could possibly be carried out.
A collaborative effort involving engineers, undergraduate college students, and superior underwater robots was orchestrated to scrub the system totally. Using specifically designed cylindrical “pigs,” enhanced with 3D printing expertise, the crew navigated the intricate community of consumption pipes with important accuracy. These automated pigs, roughly seven and a half by 5 ft in diameter and guided by subtle algorithms, guided by subtle algorithms, systematically scraped and eliminated the encrusted mussel colonies and particles with ease. This resulted in uninterrupted water move and improved cooling by way of the system.
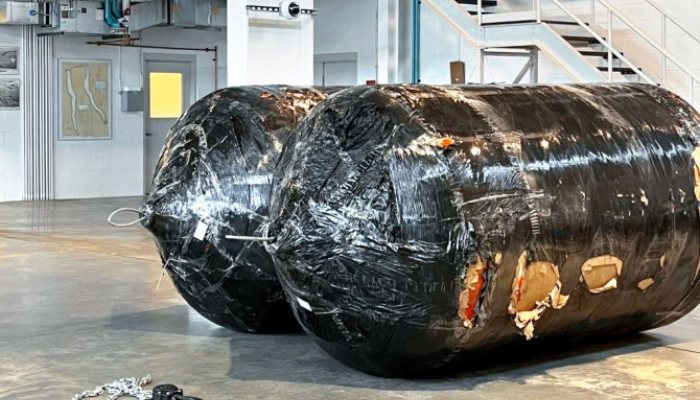
Cornell’s cylindrical “pigs”.
Cornell College’s profitable upkeep of the LSC system paves the way in which for continued sustainable cooling, with 3D printing rising as a useful device for future campus operations. With continued exploration of 3D printing applied sciences, Cornell and different establishments will doubtless set a precedent for much more artistic, sustainable options. To study extra about this undertaking, click on right here.
What do you consider Cornell’s use of 3D printing for its LSC system? Tell us in a remark beneath or on our LinkedIn, Fb, and Twitter pages! Don’t neglect to join our free weekly publication right here for the most recent 3D printing information straight to your inbox! You may also discover all our movies on our YouTube channel.
*All Photograph Credit: Cornell College